Welcome
Welcome to the June edition of the Zemax’s Community newsletter!
This newsletter provides updates for you, the user, on items you might find interesting or helpful from the last month! Check out each of these items below:
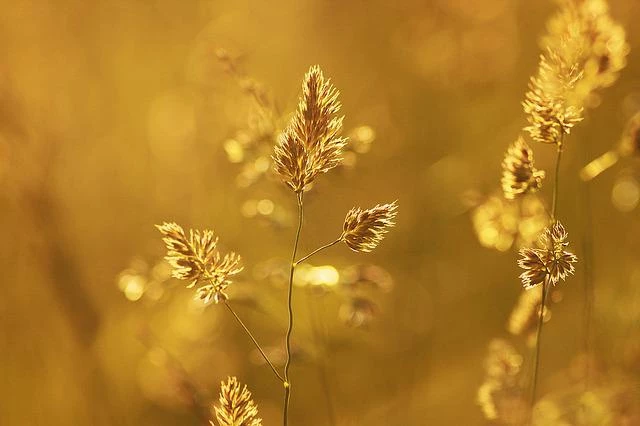
Is there something else you’d like to see? Let us know in the comments below!
Featured Community Posts: Tools for visualizing your system
This month we have selected forum posts that present ideas or macros to improve visualization. It can be visualizing the entrance pupil on a layout, seeing the propagation of a gaussian beam through an optical system or plotting the MTF in object space. Feel free to reply on these posts if you have some suggestions or feedback!
OpticsBuilder is now on OpticsAcademy!
New to OpticsBuilder, or want to increase your skills? Check out the new OpticsBuilder-focused course on OpticsAcademy! With this course, users will learn the basic concepts of optics required to package, analyze, and validate optomechanical systems. Learn how to convert your OpticStudio files into your CAD environment and analyze the system using the Zemax ray trace engine.
Get started here: Designing Optomechanical systems with Zemax OpticsBuilder
Knowledgebase Updates
- STOP Analysis of high-power laser systems - Part 3, Part 4, and Part 5
by @Julia ,@Hui Chen ,@Steven.Lacava ,@Chris Normanshire
Non-Sequential Shaded Model plot of the high-power laser system from the KBA series - Ray Geometry in OpticsBuilder
by @Flurin Herren
A demonstration of the click-able Chief Ray feature within OpticsBuilder - How to convert from Lumerical simulations to OpticStudio and back
by@Sahil
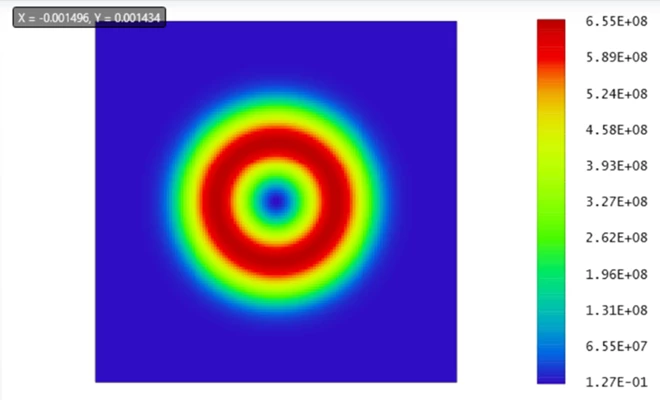
日本語ナレッジベースを拡張中! (The Japanese Knowledgebase is expanding!)
アンシス・カスタマー・エクセレンス(ACE)チームは、ナレッジベースの日本語化に注力しています。この 1ヶ月間に、日本のエンジニアは 28件のナレッジベース記事を日本語化し、現在も継続中です。日本語の記事はこちらでご覧いただけます。[日本語ヘルプ]
Zemax-er Spotlight: Paul K. Manhart
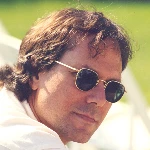
This month, we are featuring
Hide contentShow content
Tell us about yourself
I have a double major undergraduate degree in Astronomy and Physics from the University of Arizona I graduated with a Master’s degree from the Optical Sciences Center at the U of A in Tucson. I have forty-four years of experience designing optical systems for civil space and defense as well as in the commercial and consumer markets.
While at JPL, I designed optical systems for interplanetary spacecraft (Cassini telescope) and was the lead optical engineer for the Switzer Space Telescope & Instruments. I also developed technology for tolerancing segmented mirror telescopes. At Raytheon Missile Systems, I designed and developed the Advanced All-Reflective Kinetic Energy weapon for the Navy (LEAP). At LightPath Technologies, I was responsible for developing the Large-Scale axial gradient index glass (GRADIUM™️). This effort introduced the chromatic model into CodeV, ZEMAX and OSLO, as well as software development for designing & tolerancing large-scale AGRIN lenses, and developing the metrology for multi-spectral characterization of the gradient index profile.
In 2002, I chaired the International Optical Design Conference (IODC) in Tucson, AZ with Dr. Jose Sasian. Since the late 80’s I have also been active in designing optical systems for digital displays, from personal viewers to large-scale digital theaters and head worn displays for augmented and virtual reality applications. I have published over 35 technical papers in the field of optical design/engineering/metrology, and material development. I have 11 patents and 7 NASA awards for innovation.
I am an Eagle Scout, SPIE Fellow and Senior member of the OSA. I am currently working for the Department of Energy at NNSS, designing and modeling optical systems for testing nuclear weapons.
What industry trends are you excited about? Or what excites you about the optics industry in general?
After graduating with a double major in astronomy and physics, I was uncertain about what I should do. There were no jobs in astronomy and I knew I wasn't going to be a physicist. Then one day while walking around on campus, I looked up and saw Optical Sciences Center. I thought "Glass, Mirrors, Telescopes... I'm in". I knew that designing optical systems was my calling and it provided me a back door to astronomy. So I got a job at Hughes Missile Systems in Tucson and a Hughes Fellowship to get my Masters degree.
Most of my career has been designing optics for civil space (JPL and Nasa Langley), or defense (Hughes, Raytheon, Ball and others). But I've also had a lot of fabrication and metrology experience designing and building difficult optical systems. I love anything with light, especially when it's classical optics involved.
I got attracted to Virtual and Augmented reality head worn displays when I was asked by the head of neurosurgery at UCLA to help develop a helmet to replace the stereo microscope he used in neurosurgery. Then Boeing called me for another see through device to help in manufacturing aircraft. So this is a field I am interested in. I've always been of the impression that classical optics and displays will not get us there. We either need some new type of optical system (wave guides for instance), or a new display type (what I call a Pupil Display). A pupil display would be a display that requires no optics between it and the eye. Each pixel would emit light into a solid angle and each sub-angle of that would be modulated in color and power. So all the light from a distant point would appear to be collimated and hitting the eye at one angle. But this is just a dream right now. When I design something new, I always ask myself "what is the ultimate solution if materials and fabrication were not an issue". Then I try to make reality and the ideal meet somewhere.
I am also interested in the concept of form follows function. Instead of being asked to squeeze lenses into a specific volume, I first ask, "what's the best way to solve this problem"? Then and only then do we wrap metal around it.
When I started out in this business, stray light analysis was not something we did until we say a problem with the hardware. We lacked in software and we lacked in funds. We lacked in managers knowing that time spent upfront in the design process can same a lot of money down the road. Now we have the software. but we still fight the money guys because they don't understand how important stray light is to performance.
If you could offer one piece of advice to someone using OpticStudio, what would it be?
My advice to anyone using OpticStudio is this: make sure you understand optics and not just software. There is a world of difference between knowing how to operate OS and designing a good optical system. Things like looking for symmetry in design and taking advantage of it for an efficient system and package. Knowing when and where to use mirrors and lenses to your advantage. Keeping fabrication in mind during the design process is key.
At Raytheon Missile Systems, someone dumped a design on my lap one day and asked me if I could improve on it. This design had been in fabrication for 10 years and they had nothing but problems with it. The next day I showed them a design that I thought looked very promising. It reduced the part count from 48 parts down to 3. It increased the signal to noise by a factor of 3x. It cut the cost in half and reduced the alignment time from 2 weeks to half an hour. How did I do this? First, I changed the design from a catadioptric to an all reflective axial symmetric TMA (reduced the number of surfaces). Then I put the tertiary mirror on the opposite side of the primary mirror, with a secondary mirror out in front and a flat fold mirror behind. The secondary mirror was integral to the spider module. The flat mirror was integral to the rear housing and detector. This resulted in three separate modules, front, middle and rear. The sensor was about F/1 with a wide field of view and I knew tolerances would be very tight. So I transferred the burden of alignment over to the single point diamond turning lathe which is capable of holding dimensions to 1/30 millionth of an inch. The front and rear modules had annular rings that attached at the perimeter of the central primary-tertiary mirror. The optical surfaces could be diamond turned at the same time as the mechanical interfaces. This allowed for a true drop-together system, requiring zero alignment. I also went directly from the PRO-E model to the stereolith machine to make the parts in plastic. Then a foundry created molds for casting to near net shape.
I know I'm blowing my own horn here, but the point is to really think about all aspects of a design before you jump in. What are you trying to do? What are the potential problems? How will it be fabricated and aligned? What tools can you use to your advantage? Optical design is not just knowing software and programming. It's about designing a system that the customer is so happy with that he will always come back to you. It's about designing a system that makes you proud.
Are there any contributions you’ve made to Zemax in the past that others should know about?
I've been using Zemax since 1992. I found out about it from a colleague of mine at JPL (Tolis Deslis). I was working at LightPath Technologies at the time and I had just developed a dispersion model for our large scale gradient index glass. I called Ken Moore at Livermore National Labs and asked him how much it would cost to get this model put into Zemax. He quoted me a price I couldn't refuse. GRIN 5 and the gradient index controls in the MFE were my first contribution to Zemax. Within a half a year, both Code V and OSLO also had this dispersion model.
Over the past 29 years I have made many suggestions to Zemax on how they can improve both ability and ease of use in their software. I've lost track of how many of my suggestions have been implemented, but I see them pop up now and then. My current suggestion is to have a Global column in the MFE to tell what coordinate system your command refers to. An REAY with a 5 in the G column would mean that the ray coordinates are with respect to surface 5. Very simple concept and would open up global constraints in the MFE. Another is to automatically set off axis apertures by using the Footprint data. All the data is right there in Footprint to pull out the X and Y decenters and semi apertures. I think at one point I suggested they put in Kevin Thompson's Field Analysis for bi-nodal astigmatism and other aberrations. I know that function is in OS now and I'm glad it is.
What is the most challenging problem you’ve addressed with the help of OpticStudio?
This is a very tough question to answer. There have been so many modeling challenges that I've done in Zemax that it's hard to pick one out.
My latest macro was for modeling the real image quality as seen by a lens looking at a scintillator with a non zero thickness. We design the lens such that the object surface is in the center of the scintillator. But the X-Rays come from a small source and are diverging as they pass through the object and scintillator. so as each X-Ray goes through the scintillator, it leaves a trail of light. This results in an axial and lateral blur of the point spread function. So I wrote a macro that allows the user to enter the X-Ray source location and size, a dense object, a scintillator, an imaging lens and detector. I created a catalogue of fictitious glass whose properties were absorption only. I could create objects of any density I wanted and insert artifacts of different sizes and densities inside. Then as I trace a ray, it passes through the object and into the scintillator. I use a paraxial lens just before the scintillator to collimate the ray so it doesn't refract at the surface. Then, right after it enters the scintillator, I use another paraxial lens to aim it towards the entrance pupil of the lens. Then I apply a scatter surface that scatters that one ray and fills the entrance pupil with light. I step through the scintillator in 201 steps, dithering the step distance just a little bit to eliminate any periodic structure from a finite sampling. So for each ray emitted by the source, I sample 201 points along the line it makes through the scintillator. When coupled with the optical aberrations and the detector parameters, we can see whether the camera will be able to see the artifacts or not. It's a real way to determine image quality and what the scientists will see. MTF just doesn't cut it in this case. I typically trace several billion rays at a time, with a 28 core processor running at 3 GHz. I can also replace the actual lens with a paraxial lens equivalent and this allows us to see only the scintillator blur, separate from the lens aberrations.
I never would have made it through this macro if it wasn't for the help of the Zemax Technical Staff. They have been most valuable over the years and I appreciate their efforts helping me with these weird problems
What topics are you looking forward to discussing with your fellow Community members?
I would like to hear back from users what features or improvements to Zemax OpticStudio they would like to see. Do their suggestions overlap with mine, or are they totally different? The direction that Zemax is taking with their software is a good direction. But I'd like to see them pay attention to the basics also. Just plane optical design. Features and capabilities that we would like to have. Things we don't use. Ideas on better ways to do things (like apertures).
I look forward to increasing my activity in the Community Forum. I have a lot to share and a lot to learn. There are a lot of smart people out there and I'd rather ask them than struggle with it myself.
Is there anything else you would like other Zemax users to know?
I love using Zemax. But I also love using Code V. I tend to switch back and forth between the two to take advantage of their best features. I have my own way of problem solving and it always starts at the top. What's the BIG PICTURE? What's the best way to optically solve this problem? Where are my pupils and intermediate images? All first order stuff. I look at materials, fabrication, tolerance sensitivity. I look to see how I can take advantage of symmetry to simplify the system design and layout. Always start at the top and work your way down to the details, otherwise you don't see the big picture.