This forum post gives an overview on how STAR Module data can be combined with OpticStudio native environment features such as multi-configuration operands or Environment settings.
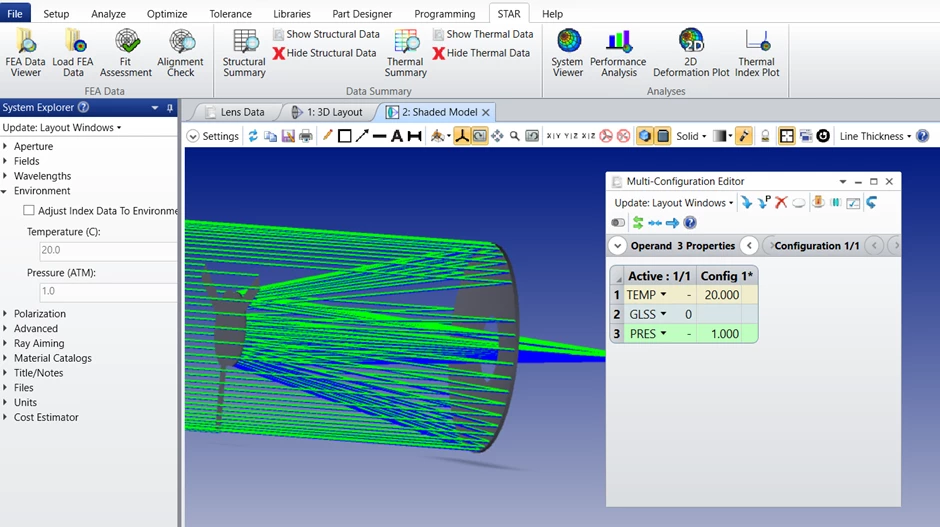
The GLSS operand should never be used on a part which has STAR temperature/index data on it, because the STAR data already contains all the index information that is needed for the part. Additionally it is also not recommend to use ROC and thickness solves to simulate temperature changes, as the STAR data is more accurate than these methods and any changes to the ROC or thickness will invalidate the STAR data on the specific part.
- In general: A Multi-Configuration system should not be used with STAR data, as STAR does not support multi-configuration yet, the workaround here would be to split the configuration into separate OpticStudio files.
For a single configuration system, the users may apply the TEMP and the PRES operand to control the temperature of any AIR surfaces present. The general air temperature, which is controlled in the System Explorer -> Environment, gives a constant temperature for the air that surrounds the parts, any changes there should be done with the TEMP and PRES operands. Users may also use the TEMP and PRES on surfaces which do not have any STAR data applied.
- In general: Users may apply TEMP, PRES and temperatures solves on any surface but surfaces which contain STAR Module dat.
Additionally, it is recommended to remove any solves before applying STAR data, so that the system is not physically changed after the STAR data is applied.