I have imported a collimator that I made in Solidworks into Zemax and started a non-sequential raytrace, I would like to send rays throughs my four lenses but can’t to figure out how to do so.
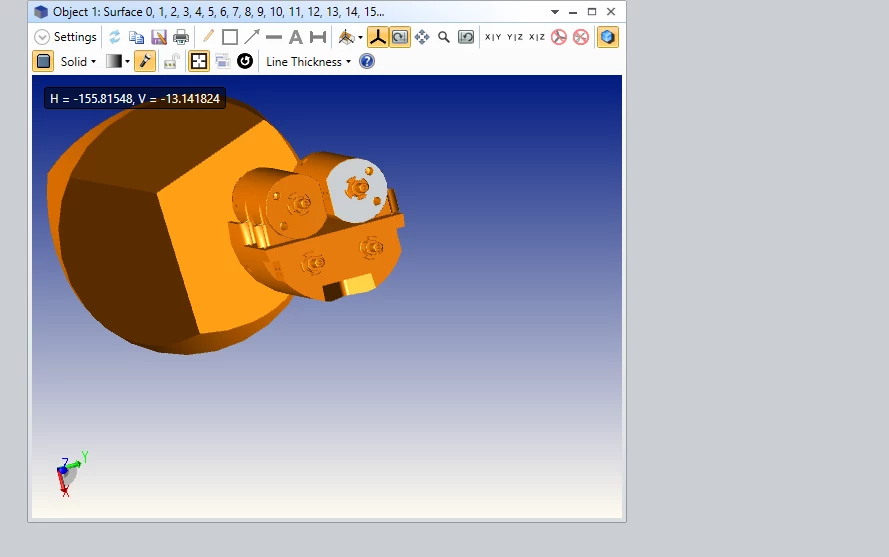
Enter your E-mail address. We'll send you an e-mail with instructions to reset your password.