Hello Zemax community!
I am an optics postgrad from New Zealand. I am not major in lens design, but genuinely interested in developing paraxial lens knowledge. I have been learning and following OpticsRealm (created by Scott) tutorial on youtube. Unfortunately, that because his tutorial was recorded over 10 years ago, it is not possible to find any solutions.
I put the question from Scott below in BOLD, and followed by my answer. I am sure some of the Pros at this community can spot some rookie issues with my approach. If you can teach me that what an optical engineer would handle this in Zemax? Massive thanks.
Refine construction of a first-order microscope in Zemax:
- Utillize paraxial lenses
- Infinity corrected with 200mm tube lens
- objective lens f=20mm
- 8 mm diagonal sensor (1/2’’ CCD)
- NA of 0.2
What is the size of object field?
(1) I planned to work “Backward” in this microscope system from 1/2’’ CCD to Tube lens, aperture stop then to the objective and finally the sample/object. The 8mm diagonal sensor has width and height of 6.4 and 4.8 mm, respectively. I chose the Surface 0 and set the Aperture to be “Rectangular”. With X-half and Y-half widths 3.2 and 2.4mm. ( I noticed that here once the rectangular is chosen, the “cross-section” diagram is no longer available. Probably it makes sense as the object/image is in 3D)
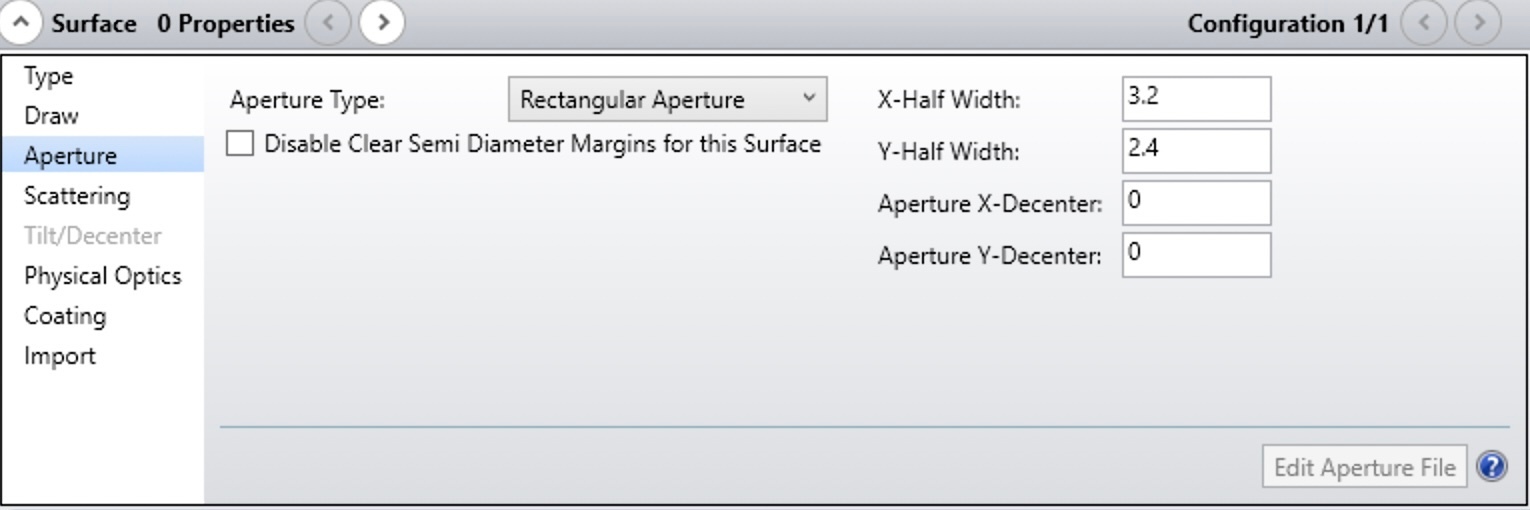
(2) With NA=2 and objective focus f=20mm. I worked out the aperture diameter in this system to be ~8.16 mm using the formula (from wiki):

The semi-diameter of the aperture therefore should be 4.08 mm as entered in surface 2:

(3) The other surfaces (paraxial lens) are also set up as the figure above. I am not showing a very nice 3D layout here as I am not quite sure how to nicely zoom in in y-axis in this 3D layout...Just put a screenshot below:
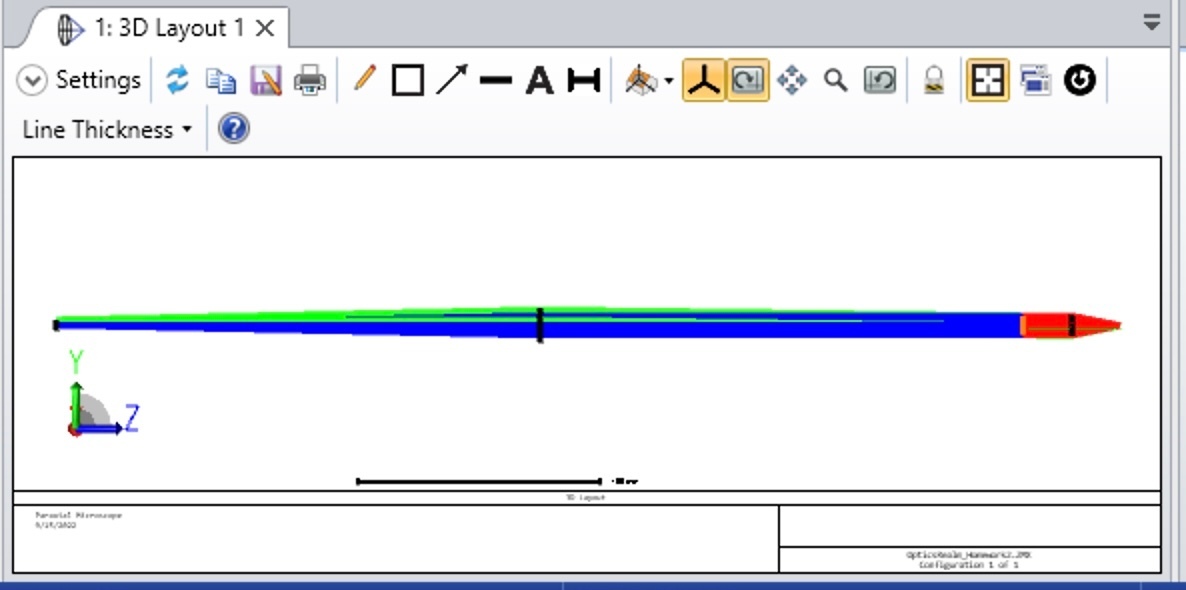
(4) The final step here is trying to find out what is the object field size. I have tried few methods, but this one is what I think a bit easy for me. Obviously, this microscope system as a magnification of 10. So I can work out the field size numerically. But it would be nice the Zemax raytrace can confirm. I chose the “standard spot diagram”. It gives the image -0.32 and -0.24 mm. It means that the size is a rectangle of 0.64 x 0.48 mm object.
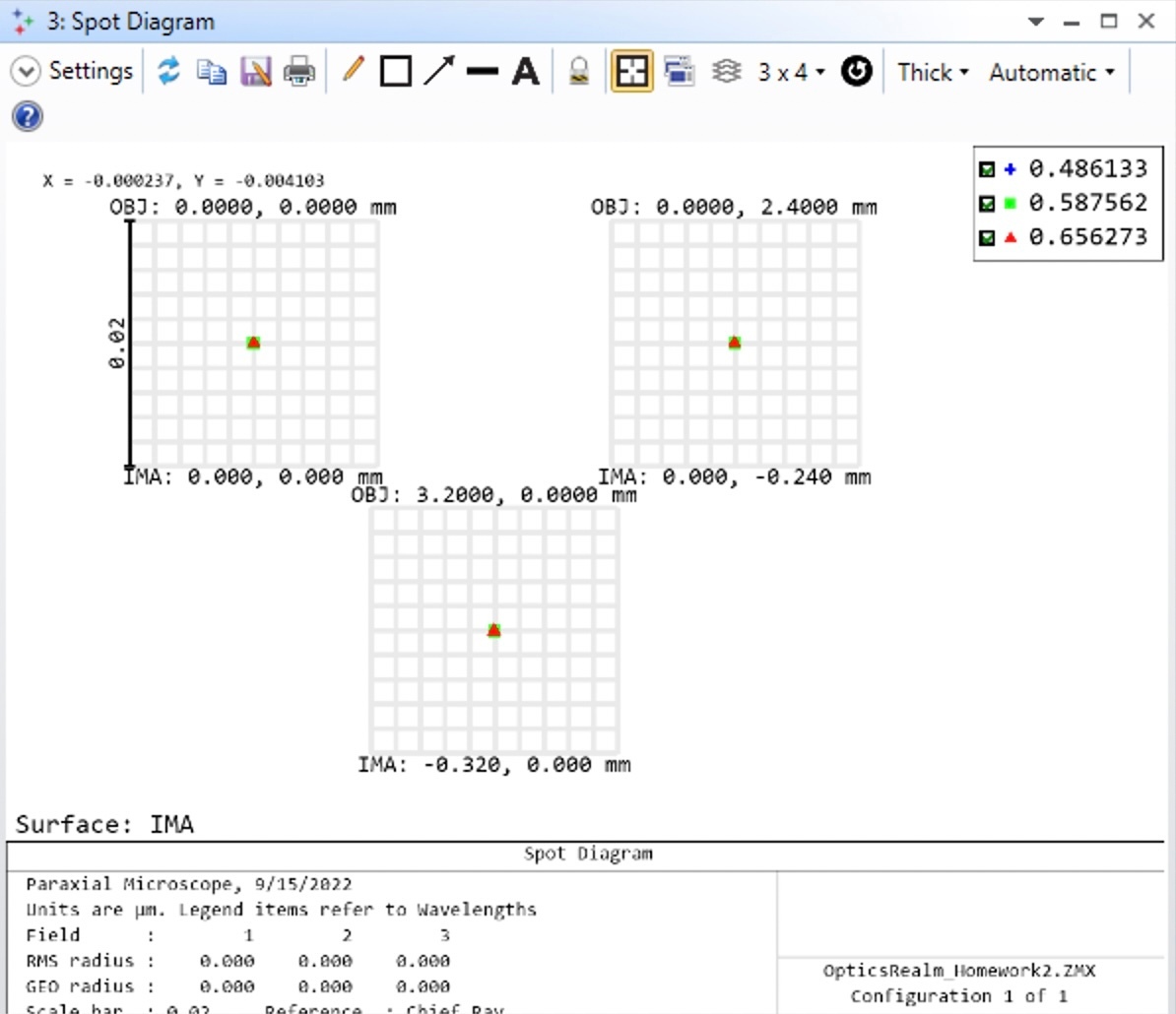
[Mod note: moved to more appropriate forum for OS-related discussions.]