Welcome
Welcome to the August edition of the Zemax’s Community newsletter!
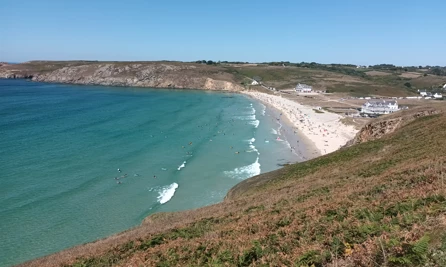
This newsletter provides updates for you, the user, on items you might find interesting or helpful from the last month! Check out each of these items below:
Is there something else you’d like to see? Let us know in the comments below!
Featured Community Posts: Heads-Up Display (HUD)
Heads-up displays are optical systems which allow information to be displayed to a user in a manner such that the user does not have to look away from their current field of view. These types of systems are particularly prevalent in the automotive industry wherein data (such as speed or remaining mileage) can be shown to a driver as a part of their windshield view. HUD systems are easily modeled in Ansys software. For example, you will see in the Knowledgebase Updates section below that OpticStudio and Speos are both powerful tools for setting up these kinds of systems. Below, we have pulled some topics on the subject to help you get started with modeling your own HUD system.
Knowledgebase Updates
Since joining Ansys, our technical team has been working on making the transition from software to software as seamless as possible. As part of that initiative, our team has published two Knowledgebase articles in the last month which demonstrate how to move from one Ansys-based optical simulation software into OpticStudio and back. Take a look below.
Ask An Engineer: How do I import a CAD component in sequential design into OpticStudio?
This month,
Zemax-er Spotlight: Mathilde Conty
This month, we are featuring

I met Mathilde during an in-person training in the UK. She then contacted the support as she was working on the non-sequential tolerancing of a laser cavity using OpticStudio and we had some interesting discussions regarding the tools.
Mathilde is a lively and friendly engineer, that always likes a bit of OpticStudio simulation in her work. To learn more about her, click Show content below.
Hide contentShow content
Tell us about yourself
I have been an engineer in optical design and in the industry for over 10 years. I have worked in various fields such as tertiary, security, defense and space.
Thus, I modelled biometric acquisition systems for security, designed lighting systems for museums and dock assist systems for Marine. I also performed the modeling and optimization of complex optronic systems with laser cavities.
I have been working for 7 years at CILAS, a company based in Orléans (France). This year, I am working on space programs as an EEE (Electrical, Electronic and Electromechanical Components) manager. I am managing the selection, evaluation and qualification of sets of opto components for space programs.
What industry trends are you excited about? Or what excites you about the optics industry in general?
Optics and optronics in general, as they offer a very wide range of possibilities in terms of applications: there is always a subject to keep you happy!
If you could offer one piece of advice to someone using OpticStudio, what would it be?
The Non-Sequential mode and Excel are your friends: if needed, the forums and the knowledge base articles are very good resources.
Are there any contributions you’ve made to Zemax in the past that others should know about?
I never made any contributions, but I often used those from other users.
What is the most challenging problem you’ve addressed with the help of OpticStudio?
Modeling a laser cavity and its optimization and sensitivity analysis thanks to various criteria. The first stage was to understand Zemax tools. I highly recommend to watch and test by yourself webinars relative to laser modeling. For this complex system, I mainly worked in Non-Sequential mode: it is well adapted to raytracing analysis and is fully defined for complex models with many rebounds.
The model had to be built against the same reference as the mechanical software (CAO) to allow a good communication between departments (optical, mechanical, thermal). The reference can be defined/imposed by a customer (most of the time it is a mechanical reference) or can also be a fictive point between the intracavity end mirror and the first face of the solid rod (medium of our cavities). The fictive point can be first associated with a simple Source ray.
That specific sensitivity analysis, in gaussian approximation, allowed to work fast and efficiently to evaluate the elementary sensitivity of each optical component inside and outside our cavities. The sensitivity was done against several parameters: misalignment, divergence, spot size, energy...
The merit function in NSC mode has some good operands such as NSDD or NSRA. Those 2 ones were the most useful to study the impact of position/tilt and manufacturing defaults of components on the optical performances.
At this point, the complexity of these models lies in the number of parameters to be studied simultaneously: in the Tolerance Data Editor (TDE), I saved each line with the SAVE operand. Then a ZPL macro would extract data from the NCS editor and the merit function. Each parameter can thus be analyzed.
The many available examples and the groups of exchanges made the ZPL macro creation fairly quick.
The Gaussian Source or Skew Source were used after to refine analyses made on the energy or the quality of the beam (M², WFE).
What do you enjoy most about OpticStudio and the Zemax Community/forums?
What I like about the software is its easy handling and the reactivity of the working groups available on the OpticStudio website and on LinkedIn. The community is involved and active. The posts are interesting and even if they do not necessarily correspond to our problem, they allow to self-train, progress, and understand all the capacities of the software.