The main issue with mixed modes is to properly define the entry and exit port. In mixed mode, the Non-sequential Component surface is the entry port whose location is determined by the previous surfaces in the Lens Data Editor. The exit port position is the same as the surface following the Non-sequential Component surface, and its location in 3D space is determined by the parameters of the Non-sequential Component surface. No objects may touch or surround the entry and exit ports.
CAD objects are defined with respect to a reference point which is the coordinate system used in CAD platform to export the object file. You may visualize the local coordinate system (reference point) of the CAD objects in the 3D layout through Object Properties...Draw as shown below:
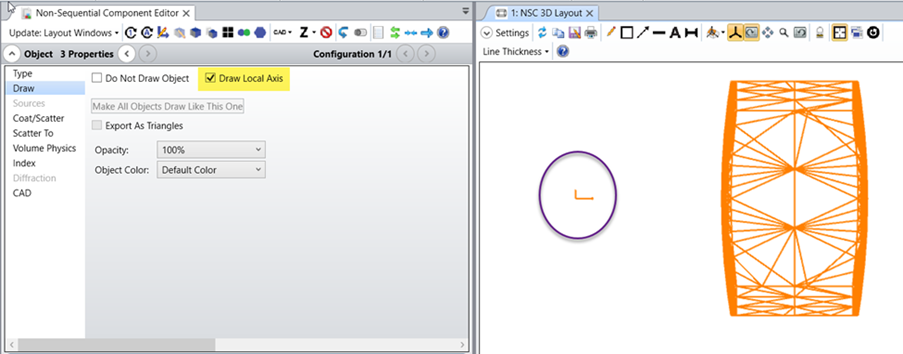
Depending on the coordinate system used in the CAD platform for file export, the CAD object might lie at a distance from the origin. When the NSC group is a CAD object, the coordinate system origin (reference point) of the CAD object cannot be in touch with entry and exit ports or lies out of the NSC group (Entry-Exit):
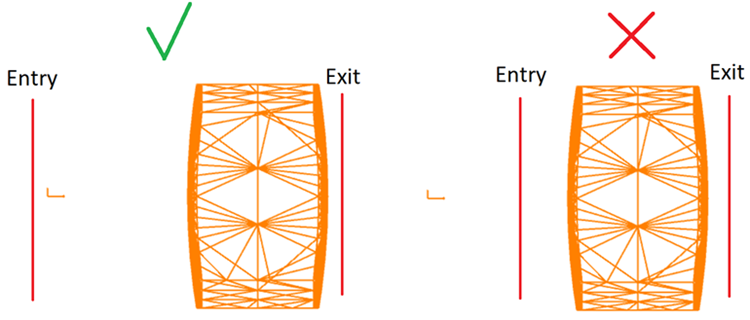
So, to place and orient CAD objects inside the NSC group, you may have two options; first you can have your mechanical engineer define a local coordinate system inside the CAD platform to properly position and orient the CAD component in the local system and then customize the STP/IGS export by selecting the defined local system; and second, you can define a Null object with your desired position and orientation in NSC mode and then refer the CAD object to the Null object.
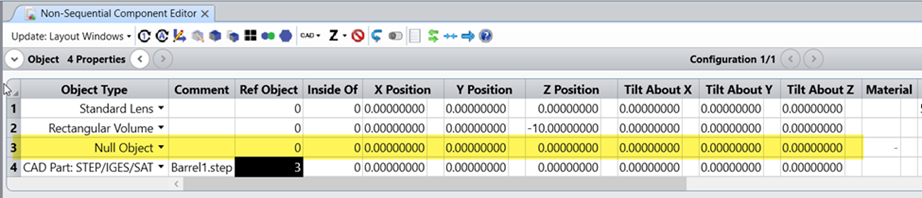
Position and Tilt parameters of the CAD objects within the NSC group set position and orientation of the CAD object local coordinate system with respect to the NSC global coordinate system, assuming the Ref. Object is 0.