Tech Tip Tuesday 5-10-22 Photolithography; a workflow with STAR & Fluent
Photolithography can be used to pattern wafers for semiconductor applications today, but it’s history goes back a lot further than that. Around the time that Joseph Niepce a French inventor created the halftone process for photography, two French printers Alfred Lemercier and Alphonse Poitevin began putting it to use experimenting with photolithography. The technique originally involved a stone plate with water and light, which is where the name comes from, it is Greek, photo = litho, and graphy = stone. The technique of photolithography would be used for engraving from the 1800’s through the 1900’s. By the 1950’s Jay Lathrop and James Nall who were working for the military at a group that would later become part of the ARL (Army Research Laboratory) would use the technique to miniaturize electronic circuits, giving us the first application of how we use it with semiconductors today.
The process used for semiconductors is typically done with a DUV source (Deep Ultraviolet laser) and ether a continuously moving liquid or a bath tank. These optical systems have the same issues with temperature change found in any laser system. Last month I wrote about using Ansys Mechanical with the OpticStudio STAR module, it works with Fluent an Ansys CFD tool too.
The use of a CFD (Computational Fluid Dynamics) software like Fluent, can be very useful for not only modeling the liquid part of these systems but also dealing with heat incident to the optics from convection currents off of other optics or objects in the system. After modeling the convection currents in Fluent. It is possible to use the results from Fluent as inputs to Mechanical to bring those temperatures and pressures in for analysis. Then with the ACT script for Mechanical the temperatures and deformations to the optical elements can be exported to STAR for use in OpticStudio.
In the image below you can see the mesh created by Mechanical on the top and Fluent on the bottom. It is also possible to use WorkBench and pass mesh data to ensure the same mesh is used across platforms, CAD geometry and input parameters can also be passed this way as discussed in my last article.
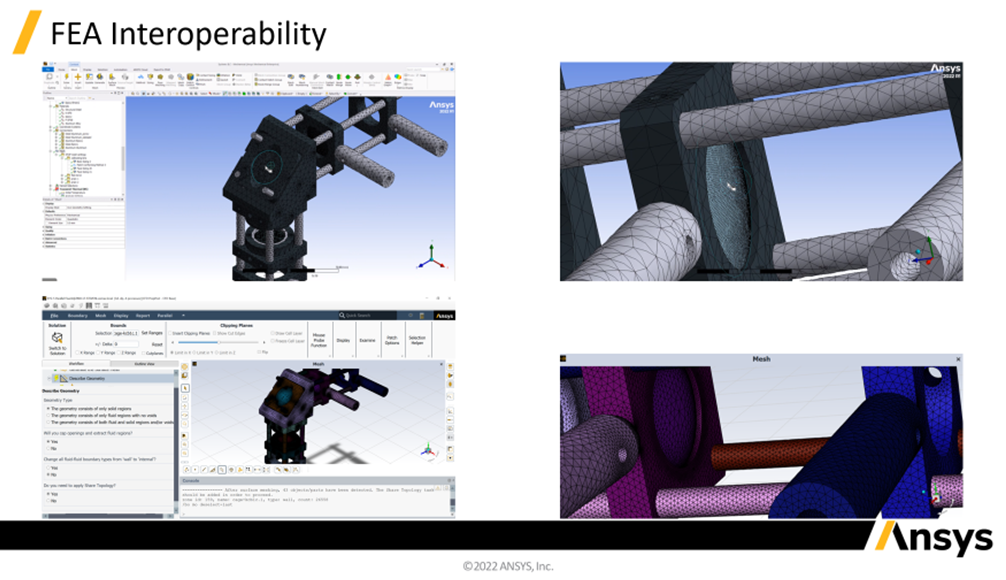
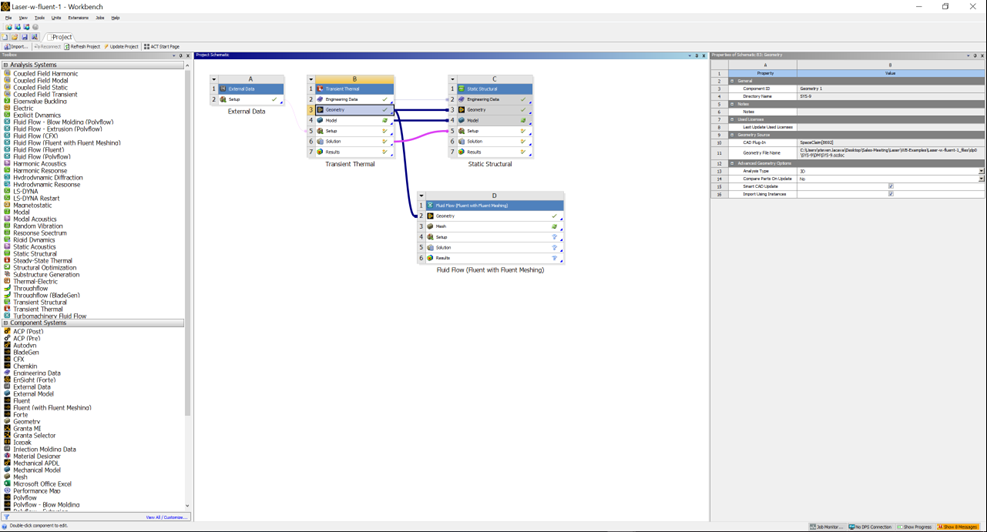
After getting the geometry and other information into Fluent, you can apply boundary conditions and define which regions are fluids and which are solids to the system. Run the calculations and analysis in Fluent, then send the results to Mechanical to use as input parameters, finally export the results to STAR to perform a STOP analysis.
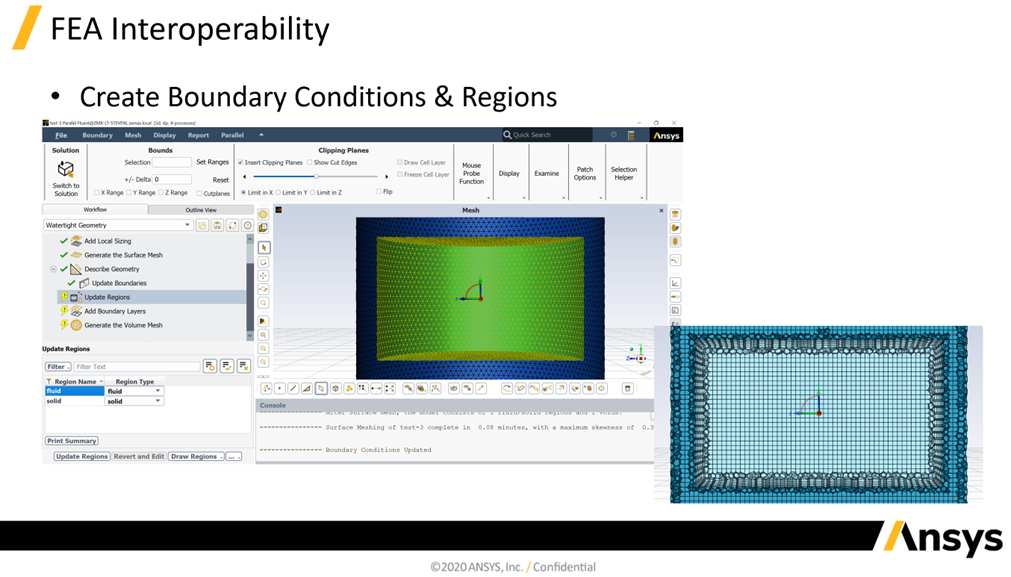
Once imported to OpticStudio via the STAR module, it is possible to conduct analysis such as deformation from the nominal design and the plot the change of refractive index as a function of the temperature. As illustrated in the images below.
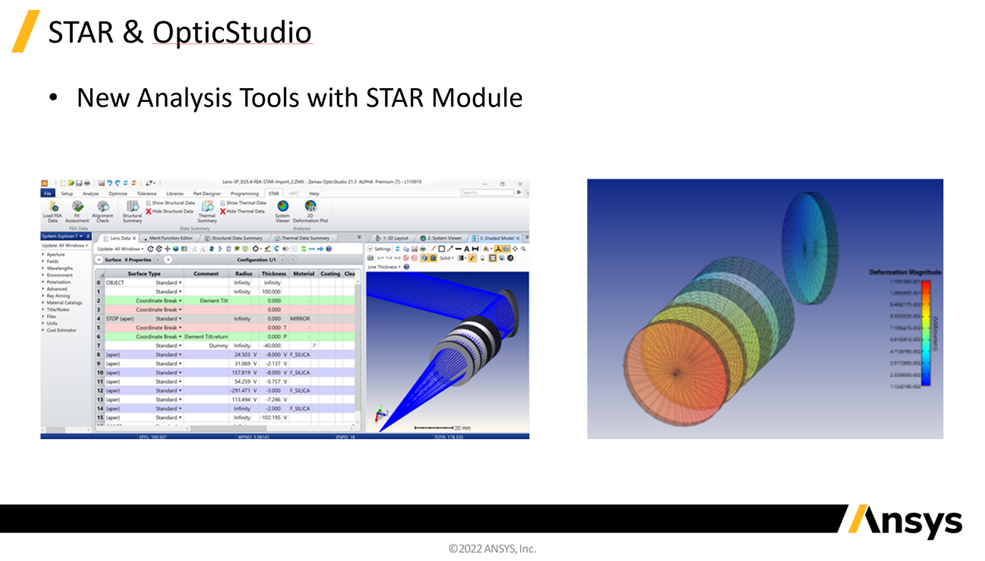
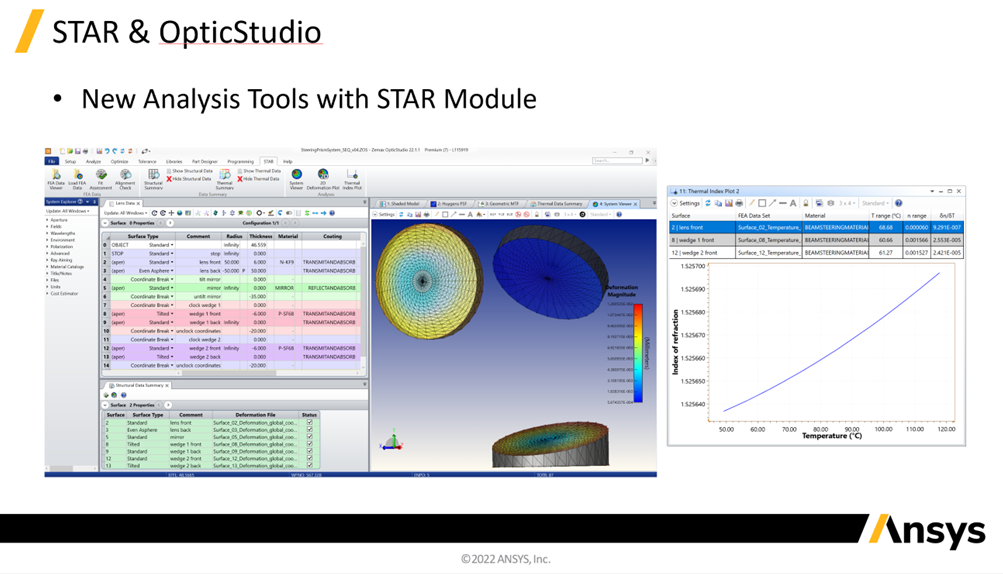
The next generation of this technology is already here, EUV (Extreme Ultraviolet) laser are used to make the paths on chips even smaller and the first commercial application of this system for semiconductor use was released to market in 2022. The physics behind these systems is considerably more complex, which may explain why it was out of reach for so long. These systems require a vacuum, multilayer mirrors, cleanroom conditions and plasmas. A very cool topic, but one we will leave for another day.
Author: Steven LaCava Senior Application Engineer
Read the Article about the use of Ansys Mechanical with the OpticStudio STAR Module
Top Tip Tuesday 4-12-22 Ansys Mechanical and OpticStudio STAR Module | Zemax Community
Learn more about the use of the ACT export script with this Knowledge Base Article
OpticStudio STAR Module: Ansys Data Export Extension – Knowledgebase (zemax.com)
An Article about Fluent and OpticStudio