Hello everyone,
I want to simulate a contact lens in Zemax OpticStudio. What I am trying to do is to create a grid sag surface with all the real data surface I have from the contact lens. I have the distance from the centre of the lens (x), the anterior and posterior radius in each point of the lens, the thickness in each point and the index of refraction. An example is depicted in the following picture:
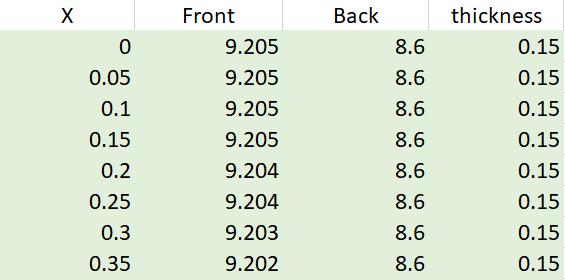
The data go until x=4mm, and this structure repeats rotationally all around the lens surface
I would like to know how I can input all this data into Zemax as a grid surface. For the moment, I know that I have to transfer the data into a matlab code (How to write a Grid Sag DAT file programmatically – Knowledgebase (zemax.com), but in this example, I can only use one value of radius, (in my case I put the posterior radius, 8.6mm). I would like to know how I can get a final file with the sag corresponding to each anterior radius (column 2 of my picture), that is varying with x, please.
In the mentioned example, the data are transferred to a square grid, but I would like to do it as a circular grid/rotationally symmetric way, as the contact lens is circular. Is it possible? I tried to change the Surface > Aperture> Circular aperture of the surface but it does not work.
The idea of what I would like to do is depicted in the picture below (just an interpretation, it is not a real surface):
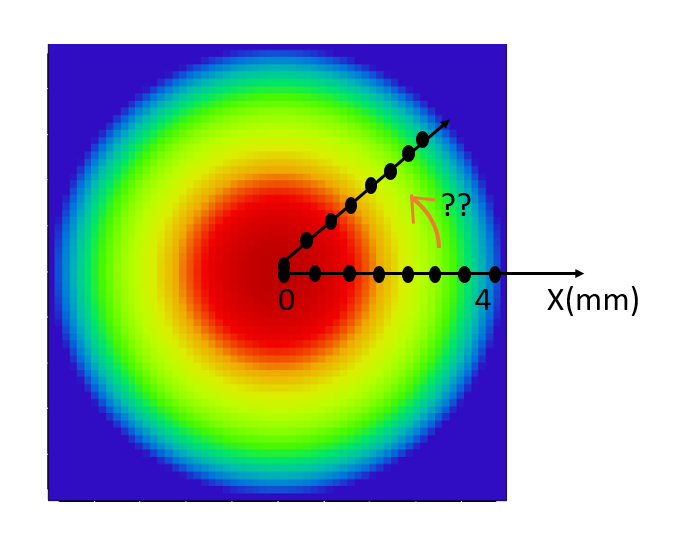
Do you think that the grid sag surface is the best for my what I need to do? If no, could you suggest me another surface type that I can use please?
Thank you very much, waiting for your answer
Alicia