OpticStudio provides two analysis tools for calculating single-mode fiber coupling efficiency. One is the Single-Mode Fiber (SMF) coupling analysis and the other is Physical Optics Propagation (POP) fiber coupling analysis. These two computation methods are based on different theories and assumptions so their results may not always agree. Which method to use will depend on your system.
POP is a wave-based light propagation tool that can be used to model laser beam diffraction propagation. The beam is represented by an array of discretely sampled points that store the complex amplitude electric field on the wavefront. The entire array is then propagated through the optical system. The physical optics model allows very detailed study of coherent optical beams, that geometric ray representation is incapable of. Single Mode Fiber coupling analysis uses rays to represent the beam propagation from object surface to the exit pupil and only considers diffraction effect from exit pupil to image plane, which is what we call the “single step” approximation. This is the main difference between POP and SMF coupling analysis.
Though powerful POP algorithm has one limitation. It’s the difficulty in handling fast beams. POP is based on scalar diffraction theory which may break down when the beam is very fast. When this happens POP issues a warning in the Propagation Report, “Pilot beam waist smaller than wavelength!”. This is one indication that the beam is too fast to be accurately modeled by POP. For fast beams ray representation is generally a better approach. You can either switch to ray-based analysis or tick the Use Rays To Propagate To Next Surface box under Surface Properties\Physical Optics to address this issue.
Depending on the system, designer needs to decide which tool is more suitable for your application. There are three scenarios we normally recommend using POP. You can find them listed in the help file, The Analyze Tab (sequential ui mode) > Laser and Fibers Group > About Physical Optics Propagation
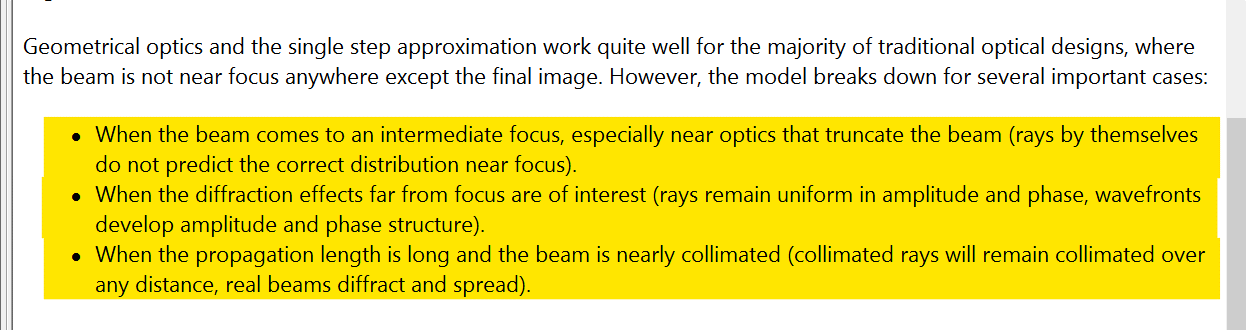
If your system is one of these three cases where POP is needed, very likely you will observe different coupling efficiency reported between SMF coupling analysis and POP coupling analysis. For these cases, POP should be the intended tool for coupling analysis.
Next, I’ll show you a couple examples that compare these two fiber coupling analyses.
Case 1: A singlet conic lens to couple light between two fibers.
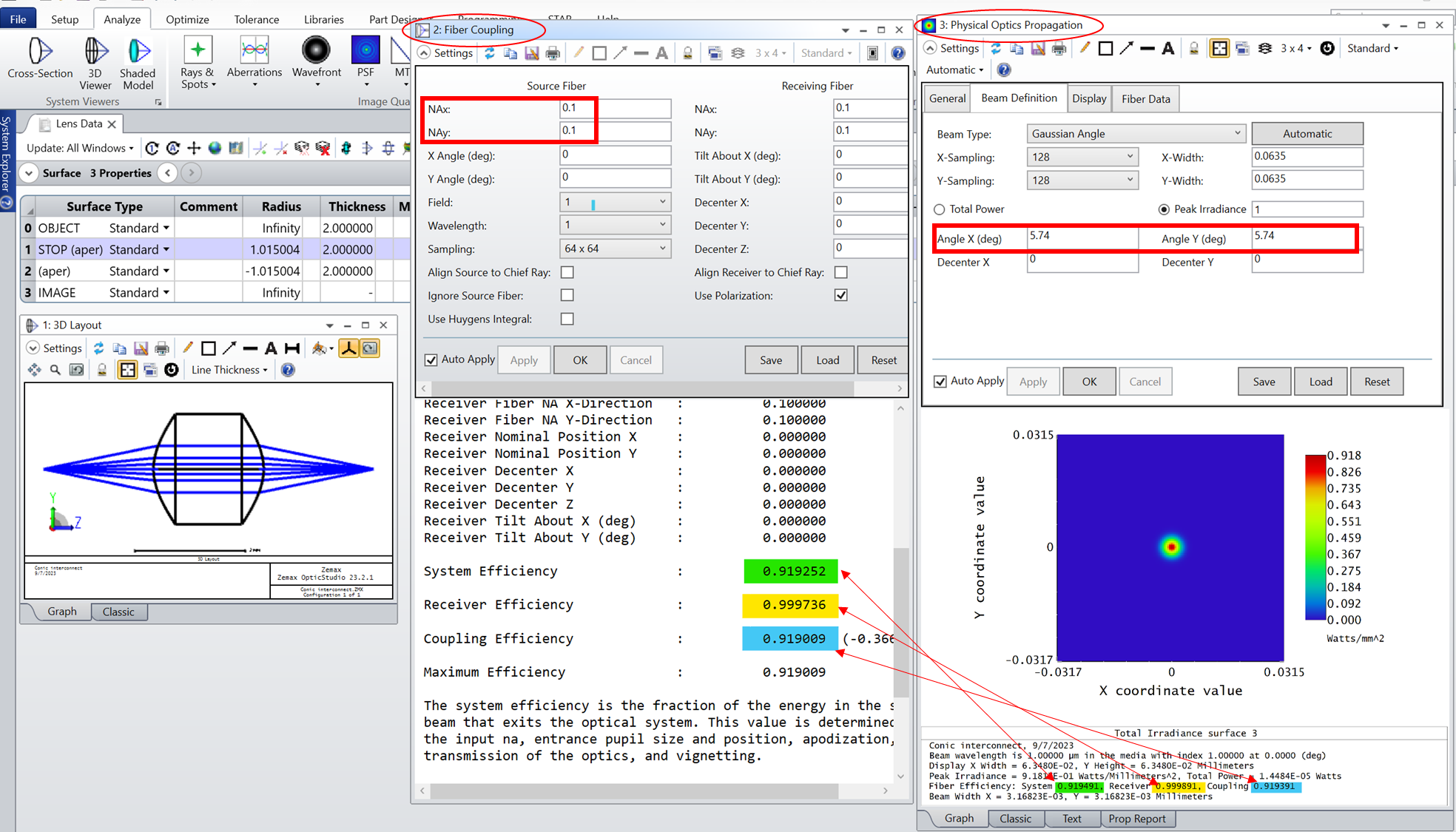
In this case both SMF coupling and POP fiber coupling analyses work, and when entering the same beam divergence angle for the input fiber and receiving fiber mode, the two analyses give very similar results for coupling efficiency.
Case 2: Two lenses system to couple from fiber to fiber with a long, nearly collimated propagation between the two lenses.
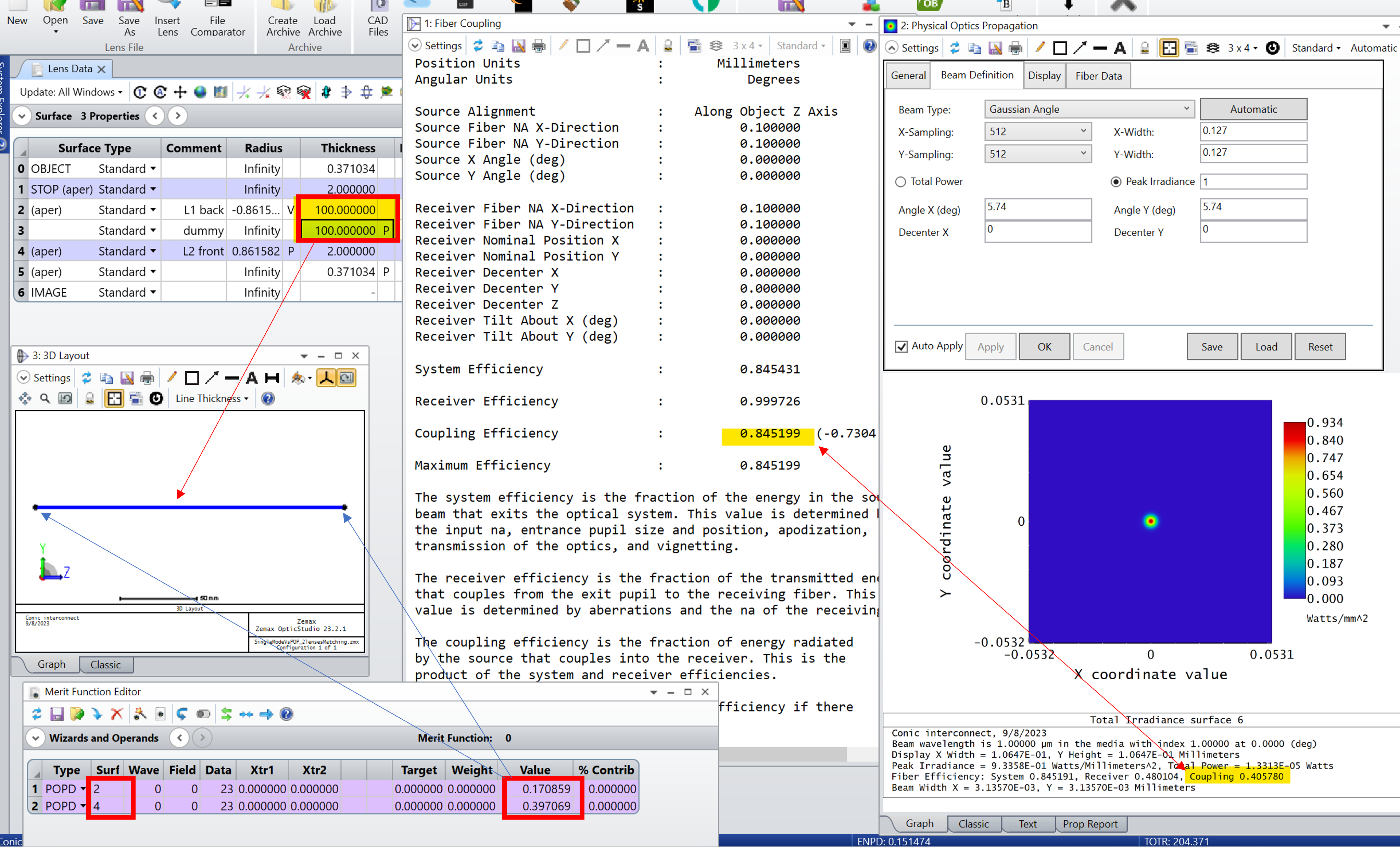
Due to this long, collimated beam propagation, POP and SMF yield very different coupling efficiency, with POP efficiency only about half of what SMF reports. In this case POP analysis should be used, because geometric ray representation cannot accurately model this long, nearly collimated propagation. Collimated ray bundle remains collimated, and the beam size barely changes between surface 2 (back of L1) and surface 4 (front of L2) if you look at the Spot Diagram on these two surfaces. However, laser beam diffracts as it propagates, and beam size always changes. In the merit function editor, if we use POPD operand to report beam size at surface 2 and 4, you’ll see it’s almost doubled after this long propagation. This diffraction propagation of the laser beam cannot be accurately modeled by ray representation, therefore in this case SMF coupling efficiency result may be overly optimistic and POP is more accurate.
These are just two simple examples for demonstration. Which analysis tool is better suited for your application may need careful evaluation. If you would like to know more about single mode fiber coupling analysis in OpticStudio, I recommend this KBA written by Mark Nicholson and Kristen Norton, Single-mode fiber coupling in OpticStudio – Knowledgebase (zemax.com). If you need help setting up the analysis or understanding the results, please feel free to contact Ansys Zemax support team. Our ACE engineers are always ready to assist you.