Hi all!
I have done user defined dll surface and want to check its accuracy. For this, I did a lens with such surface on one side and plane on the other in SolidWorks and opened it like .STEP file as a non-sequential component. In the second Zemax file, I opened my user-defined dll. All dimensions, apertures the same. Also, I can see that rays go through the lens in almost the same way. Spot diagrams look very similar. But I want to compare the wavefront map and here I have a huge difference also ray fan very different and I cant understand the reason. It's my first time with non-sequential mode, maybe someone can help me with good advice? Thank you a lot
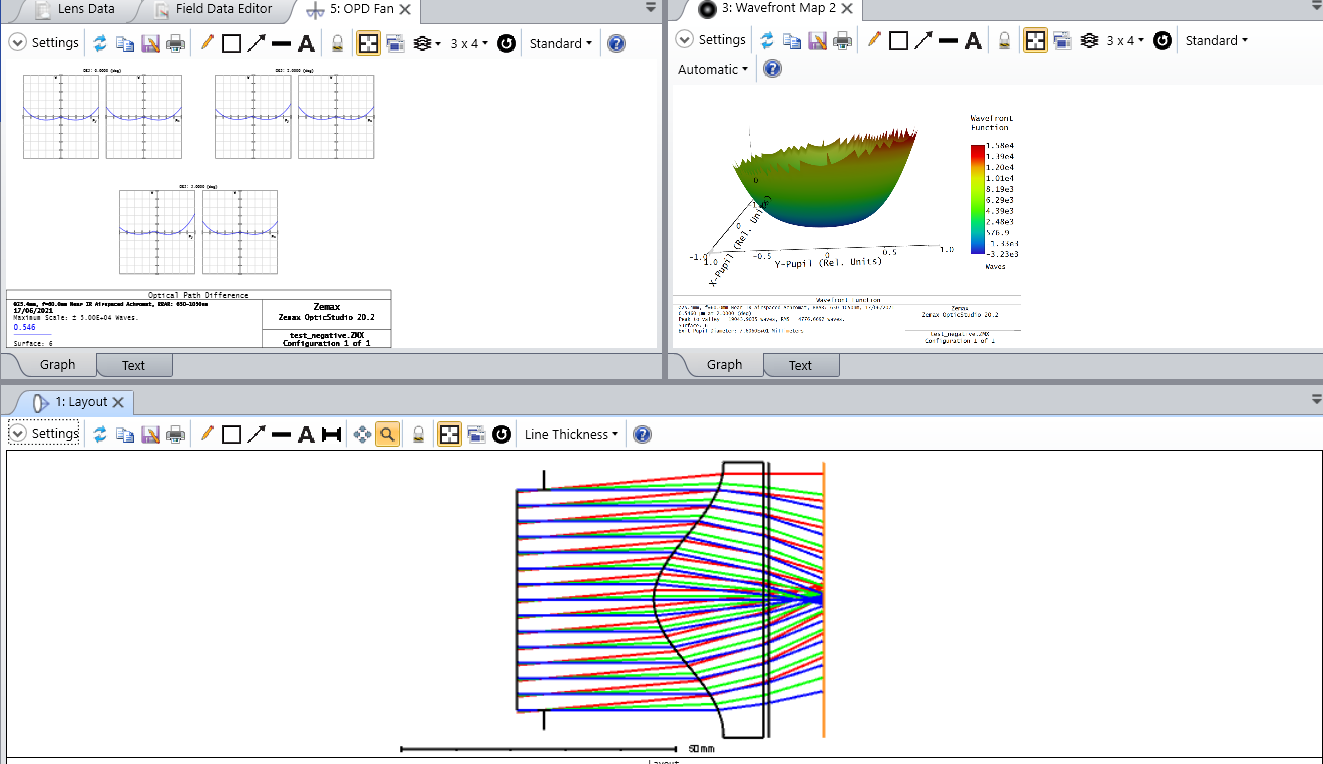
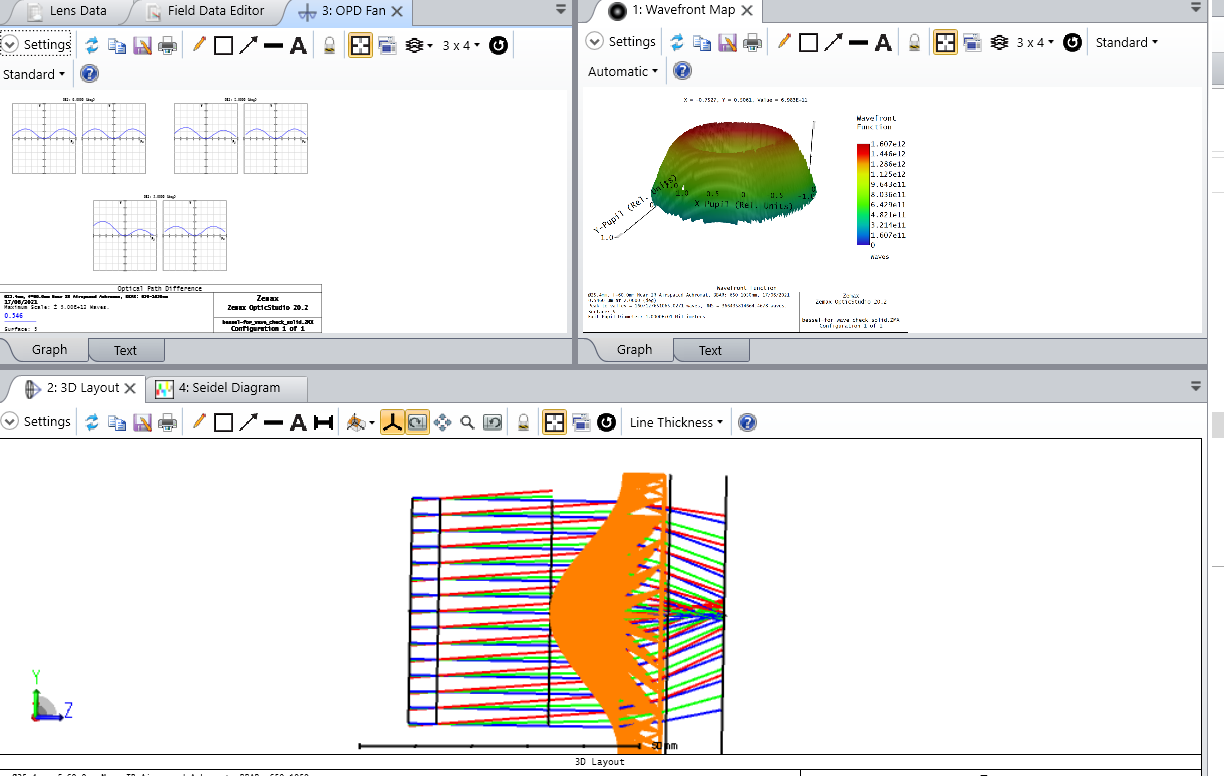